Electric Vehicle Battery is Composed of :
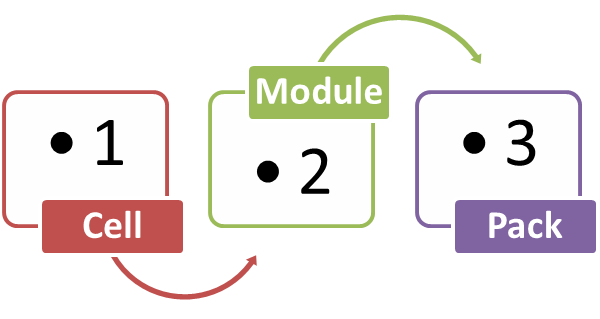
The complete battery system (3), consists of large-format Li-ion cells (1); modules (2) comprising multiple cells; and of an integrated battery management system that provides a communication interface to the host system and the peripherals.

Our manufactures all the components of the system in-house. Based on scalable design, the European Batteries cell modules and systems can be conveniently adapted to various customer needs in terms of voltage, capacity and energy. The same overall structure is suitable for transport, heavy industrial
machines and energy storage purposes alike.
Industry-leading cell production knowledge European Batteries uses lithium iron phosphate as raw material for their cells. This provides a combination of advantages, unmatched by any other lithium-ion chemistry:
• Very high energy density
• Very long life (both cycle and calendar life)
• Improved safety
• Eco-friendliness of the used materials
Lithium iron phosphate (LiFePO 4 or LFP) is the newest of the Li-ion cathode materials. Compared to other materials such as LCO, LFP
provides longer cycle-life and in better thermal stability – thus being a substantially safer alternative.
Scalable design
The EBatteryproduct family includes several modules, each consisting of multiple battery cells and featuring different combinations of voltage and capacity. Utilizing same basic components makes module production and assembly prompt and efficient. The variety, on the other hand, enables numerous tailoring options for application-specific systems.

A perfect fit for any purpose
Cars Modular structure and scalable design also allow placing the modules in the most efficient way for any space, situation or purpose. For example, T-shaped battery packs have been designed to efficiently utilize the space in a vehicle.
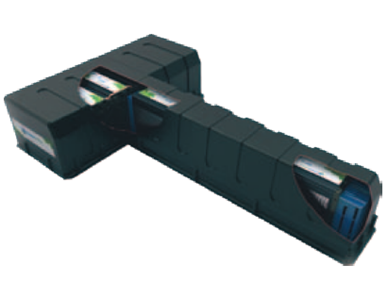
Heavy vehicles Utilizing the available space and uncontested energy density per weight ratio, efficient solutions can be created even for larger vehicles and industrial machines.
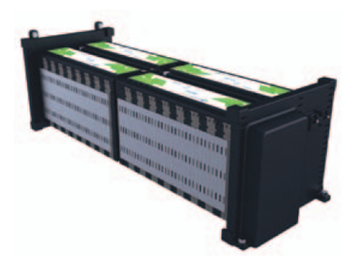
Marine The advanced design allows even large MWh size systems based on packs in parallel connection – strong enough to be used in marine and demanding offshore applications. The systems of this caliber require converters or active line units.
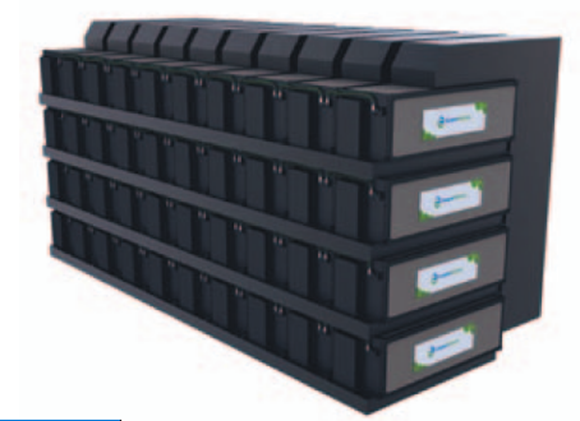
Energy Storage Whether they are used to store larger amounts of energy for undefined future purposes or to equip heavy machinery with efficient energy storages, packs and systems can be scaled up to a point where they fill an entire container.
Advanced battery management system for purpose-specific efficiency
Our factory solution always comes with integrated battery management system. This system ensures flawless operation of the solution by carrying out several tasks such as:
• Monitoring and controlling critical parameters such as cell voltages and module temperature
• Maximizing available capacity, energy efficiency and the cycle life of the battery system
• Controlling charging regime.
• Keeping the cells on equal state-of-charge level
• Providing a communication interface to the host system
• Ensuring high balancing current, scalability and intelligent balancing algorithm
The battery management master unit has a wide variety of advanced features, such as:
• Interfaces to the host system: CAN, Ethernet, RS232, RS485, FO serial interface and USB for service
• Supported protocols: CAN Open battery profile. Modbus and Profinet with gateway option
• Isolated battery stack insulation level monitor
• Flash memory for data logging
• Integrated power unit (up to 1.0 kV stack voltage)
• Several contactor driving outputs and relay outputs
• Several isolated analog and digital inputs/outputs
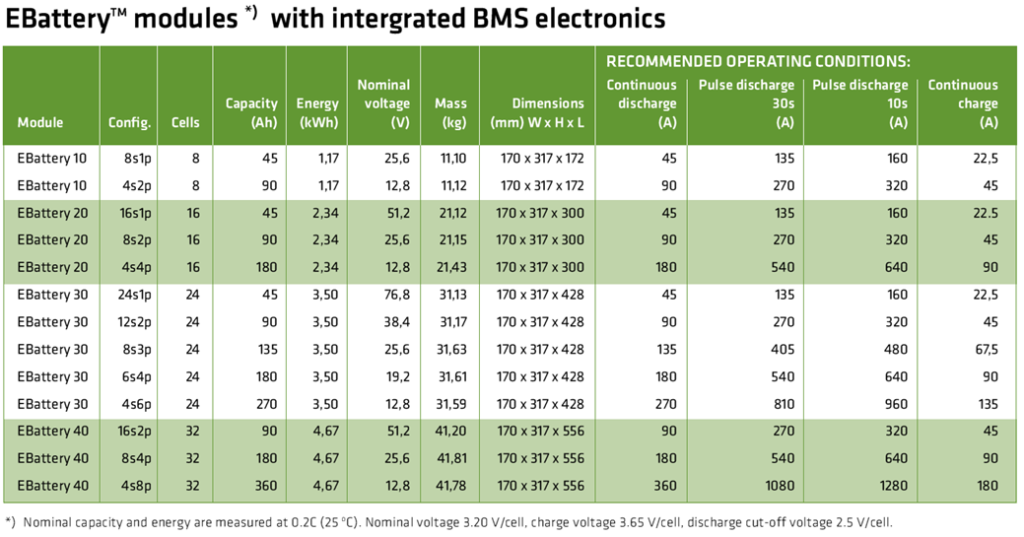

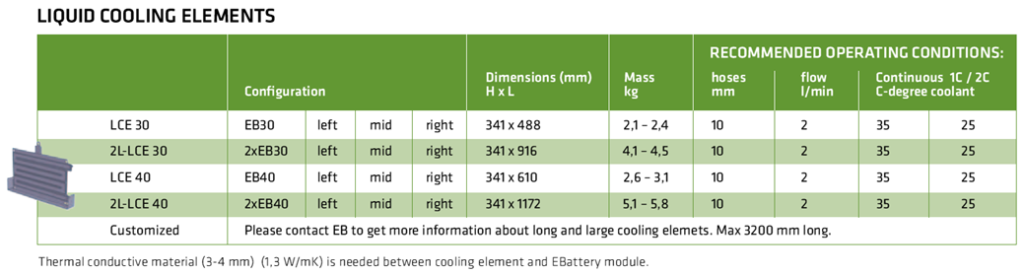
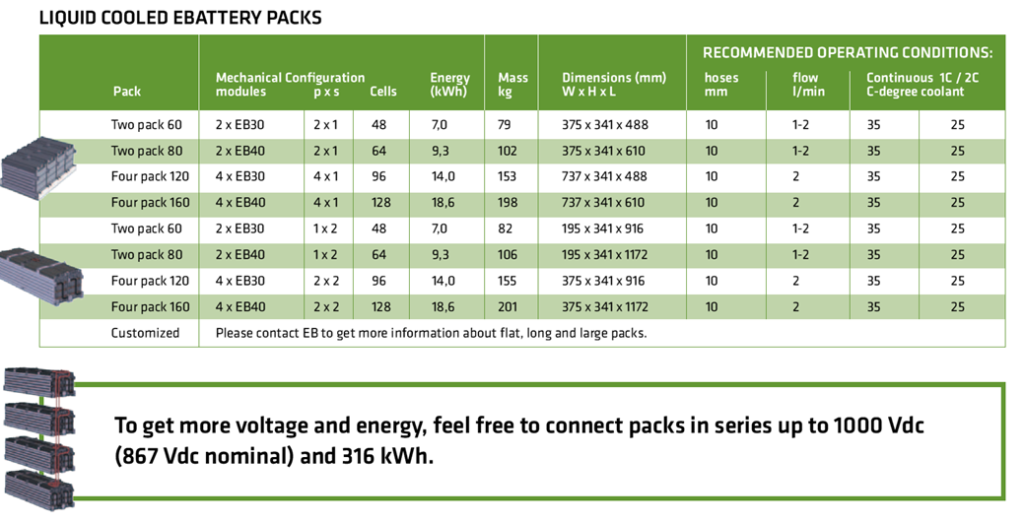

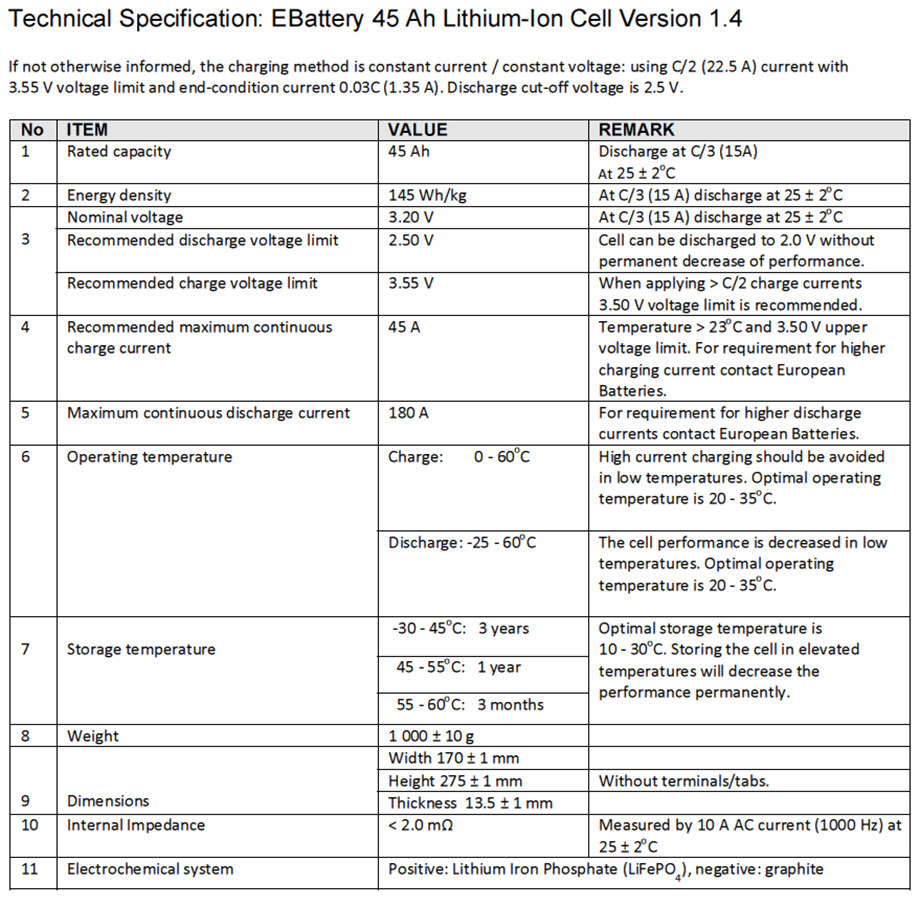
There are no stander battery package, battery is designed depended on the application! Power, Size, charging…etc
EVB battery for Vehicles
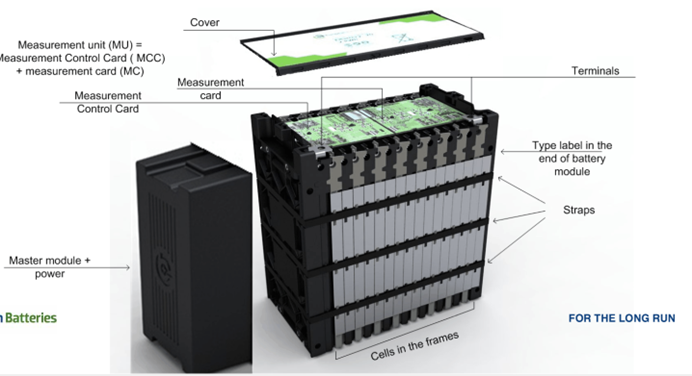
2. Technical specification and application for fast charging
Most lithium-ion battery pack designs involving cylindrical, pouch or prismatic automotive cell types can be realized as:
1. Cylindrical battery cells
Clamshell battery designs are suitable for increased energy storage and usually involve cylindrical cell types, which are normally fixed in place using adhesives, the curing of the adhesives can be completed in just five seconds. This, in turn, significantly speeds up battery module assembly.
2. Prismatic battery cells
In prismatic cell types is typically used for busbar holders due to its properties. This is especially suitable for heavy-duty e-vehicles such as electric buses and electric trucks.For designs requiring long-term vibration tests.
3. Pouch battery cells
Due to their geometry, pouch cell types are easy to fit into tight spaces, but battery packaging designs must also account for swelling during charge and discharge cycles. Frames must also satisfy the need for precision molding.
The volume of each cell is calculated as:
- cylindrical cells, Vcc [m3]
Vcc=πD2bc4⋅Lbc(1)
where:
Dbc [m] – battery cell diameter
Lbc [m] – battery cell length
- pouch cells, Vpc [m3]
Vpc=Hbc⋅Wbc⋅Tbc(2)
where:
Hbc [m] – battery cell height
Wbc [m] – battery cell width
Tbc [m] – battery cell thickness
The battery cell energy Ebc [Wh] is calculated as:
Ebc=Cbc⋅Ubc(3)
where:
Cbc [Ah] – battery cell capacity
Ubc [V] – battery cell voltage
The battery cell energy density is calculated as:
- volumetric energy density, uV [Wh/m3]
uV=EbcVcc(pc)(4)
- gravimetric energy density, uG [Wh/kg]
uG=Ebcmbc(5)
where:
mbc [kg] – battery cell mass
The energy density for each cells are summarised in the table below.
Manufacturer | ||||||
Type | cylindrical | cylindrical | cylindrical | pouch | pouch | pouch |
Model | NCR18650B | ANR26650m1-B | ICR-18650K | 20Ah | 20Ah | SLPB7570270 |
Energy [Wh] | 11.52 | 8.25 | 9.62 | 64.35 | 46 | 56.16 |
Volume [l] | 0.017553 | 0.034510 | 0.017716 | 0.263320 | 0.260590 | 0.171741 |
Energy density gravimetric [Wh/kg] | 237.53 | 108.55 | 192.40 | 129.74 | 90.20 | 177.16 |
Energy density volumetric [Wh/l] | 656.31 | 239.06 | 543.01 | 244.38 | 176.52 | 327 |
In order to have a better overview of the cells parameters and to compare them easier, the main parameters are displayed as bar graphs in the images below.
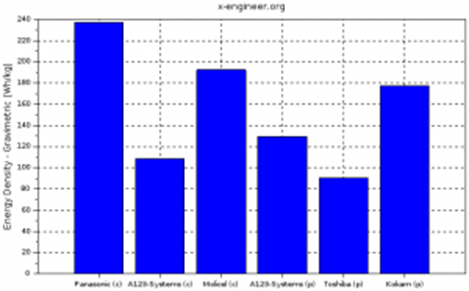
With the above cell parameters and the core requirements for the battery (nominal voltage, average energy consumption and vehicle range), we calculate the main parameters of the high voltage battery.
The required battery pack total energy Ebp [Wh] is calculated as the product between the average energy consumption Eavg [Wh/km] and vehicle range Dv [km]. For this example we’ll design the high voltage battery pack for a vehicle range of 250 km.
Ebp=Eavg⋅Dv=161.7451⋅250=40436.275 Wh=40.44 kWh(6)
The following calculations are going to be performed for each cell type. For this example we are going to consider that the battery pack is made up only from several strings connected in parallel.
The number of battery cells connected in series Ncs [-] in a string is calculated by dividing the nominal battery pack voltage Ubp [V] to the voltage of each battery cell Ubc [V]. The number of strings must be an integer. Therefore, the result of the calculation is rounded to the higher integer.
Ncs=UbpUbc(7)
The energy content of a string Ebs [Wh] is equal with the product between the number of battery cells connected in series Ncs [-] and the energy of a battery cell Ebc [Wh].
Ebs=Ncs⋅Ebc(8)
The total number of strings of the battery pack Nsb [-] is calculated by dividing the battery pack total energy Ebp [Wh] to the energy content of a string Ebs [Wh]. The number of strings must be an integer. Therefore, the result of the calculation is rounded to the higher integer.
Nsb=EbpEbs(9)
We can now recalculate the battery pack total energy Ebp [Wh] as the product between number of strings Nsb [-] and the energy content of each string Ebs [Wh].
Ebp=Nsb⋅Ebs(10)
The battery pack capacity Cbp [Ah] is calculated as the product between the number of strings Nsb [-] and the capacity of the battery cell Cbc [Ah].
Cbp=Nsb⋅Cbc(11)
The total number of cells of the battery pack Ncb [-] is calculated as the product between the number of strings Nsb [-] and the number of cells in a string Ncs [-].
Ncb=Nsb⋅Ncs(12)
The size and mass of the high voltage battery are very important parameter to consider when designing a battery electric vehicle (BEV). In this example we are going to caclulate the volume of the battery pack considering only the battery cells. In reality there are other factors to consider, like: electronic circuits, cooling circuit, battery casing, wiring, etc.
The battery pack mass (cells only) mbp [kg] is the product between the total number of cells Ncb [-] and the mass of each battery cell mbc [kg].
mbp=Ncb⋅mbc(13)
The volume of the battery pack (cells only) Vbp [m3] is the product between the total number of cells Ncb [-] and the mass of each battery cell Vcc(pc) [m3]. This volume is only used to estimate the final volume of the battery pack, since it does not take into account the auxiliary components/systems of the battery.
Vbp=Ncb⋅Vcc(pc)(14)
The volume can be also calculated function of number of strings and number of cells in a string. This calculation method is more appropriate for cylindrical cell, since the volume occupied by a cylindrical cell must take into account the air gap between cells.
The string peak current Ispc [A] is the product between the peak C-rate of the battery cell C-ratebcp [h-1] and the battery cell capacity Cbc [Ah].
Ispc=C-ratebcp⋅Cbc(15)
The battery pack peak current Ibpp [A] is the product between the string peak current Ispc [A] and the number of strings of the battery pack Nsb [-].
Ibpp=Ispc⋅Nsb(16)
The battery pack peak power Pbpp [W] is the product between battery pack peak current Ibpp [A] and the battery pack voltage Ubp [V].
Pbpp=Ibpp⋅Ubp(17)
The string continuous current Iscc [A] is the product between the continuous C-rate of the battery cell C-ratebcc [h-1] and the battery cell capacity Cbc [Ah].
Iscc=C-ratebcc⋅Cbc(18)
The battery pack continuous current Ibpc [A] is the product between the string continuous current Iscc [A] and the number of strings of the battery pack Nsb [-].
Ibpc=Iscc⋅Nsb(19)
The battery pack continuous power Pbpc [W] is the product between battery pack continuous current Ibpc [A] and the battery pack voltage Ubp [V].
Pbpc=Ibpc⋅Ubp(20)
The results of the equations (7) to (20) are summarised in the table below.Manufacturer | ||||||
# of cells in string [-] | 112 | 122 | 109 | 122 | 174 | 112 |
String energy [Wh] | 1290 | 1007 | 1049 | 7851 | 8004 | 6290 |
# of strings [-] | 32 | 41 | 39 | 6 | 6 | 7 |
BP energy [kWh] | 41.29 | 41.27 | 40.89 | 47.10 | 48.02 | 44.03 |
BP capacity [Ah] | 102.4 | 102.5 | 101.4 | 117 | 120 | 109.2 |
# total cells [-] | 3584 | 5002 | 4251 | 732 | 1044 | 784 |
BP mass [kg]* | 173.8 | 380.2 | 212.6 | 363.1 | 532.4 | 248.5 |
BP volume [l]* | 63 | 173 | 75 | 193 | 272 | 135 |
BP peak current [A] | 102.4 | 2460 | 202.8 | 1170 | 120 | 327.6 |
BP peak power [kW] | 40.96 | 984 | 81.12 | 468 | 48 | 131.04 |
BP continuous current [A] | 102.4 | 1025 | 101.4 | 117 | 120 | 218.4 |
BP continuous power [kW] | 40.96 | 410 | 40.56 | 46.8 | 48 | 87.36 |
BP – battery pack
* – taking into account only battery cells
From the table data we can see that the pouch type cell have better energy content and higher capacity compared with the cylindrical cells.
The same results can be plotted in bar graphs for an easier comparison between the different types of battery cells.
Because of the low capacity for the cylindrical cells, compared to the pouch cells, the number of cells required for the battery pack is significant higher. A high number of cells might cause additional problems in areas of wiring, voltage monitoring, battery reliability.
The mass and volume are calculated only at cell level, taking into account the cell dimensions and mass. The battery pack which will be in the vehicle will have additional components (wires, electronic components, soldering, case, etc.), which will increase both the final volume and mass. Nevertheless by looking only at cell based volume and mass, we can estimate which model will be better compared to the other. In terms of mass and volume there is no clear distinction between cylindrical and pouch cells. However it seems that a battery pack with pouch cells is slightly heavier and bigger.
The battery cells manufactured by A123-Systems have very high maximum continuous discharge current and maximum pulse (peak) discharge current. As for energy and capacity, the pouch type cells have higher peak (continuous) current and power than cylindrical cells.
Based on the calculated data and conclusions, we can choose which battery cells are suitable for our electric vehicle battery pack. From our examples it looks like Kokam cells have the best compromise between mass, volume and energy/power density.
EV Battery Cooling System
This demo shows an Electric Vehicle (EV) battery cooling system. The battery packs are located on top of a cold plate which consists of cooling channels to direct the cooling liquid flow below the battery packs. The heat absorbed by the cooling liquid is transported to the Heating-Cooling Unit. The Heating-Cooling Unit consists of three branches to switch operating modes to cool and heat the battery. The Heater represents an electrical heater for fast heating of the batteries under low temperature conditions. The Radiator uses air-cooling and/or heating when the batteries are operated stably. The Refrigerant system is used for cooling the overheated batteries. The refrigeration cycle is represented by the amount of heat flow extracted from the cooling liquid. The system is simulated under either FTP-75 drive cycle or fast charge scenarios with different environment temperatures.
Battery is customized according to the application:
*The bus battery are 50 Kwh, 70Kwh, 150 Kwh